|
Author |
Message |
NigelT
Site Admin
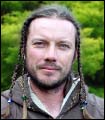
Location: Wellington
|
Posted: Mon Jan 08, 2007 7:55 pm Welding spring steel |
|
|
Hi all,
One of my pet projects (which I've not got around to starting for some time now) is to make a Zweihander sword, complete with catching lugs on the blade.
My problem is this - how do I attach the blade lugs without badly affecting the strength of the blade through the subsequent tempering process? Is it a simple matter of arc welding using low hydrogen rods or does this need to be forge welded, or some other process. The blade will be high carbon spring steel.
Any thoughts?
Nigel |
|
|
 |
Colin
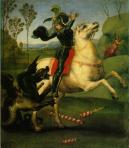
Location: Wellington
|
Posted: Mon Jan 08, 2007 10:49 pm |
|
|
Arrgh! Never use any form of welding on (high carbon) steel! You will create stress points on either side of the weld, and then you can kiss your blade goodbye.
If you want lugs you're going to have to have there before you get it tempered. |
|
|
 |
Angel
Site Admin
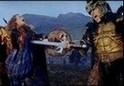
Location: Wellington
|
Posted: Tue Jan 09, 2007 9:00 am |
|
|
The lugs will need to be cut as part of the blade. Weld them on and they'll come flying off again in pretty short order, not to mention the welding will f**k the temper on the blade, and it'll snap at that spot. _________________ Recognise anyone? Flame Warriors |
|
|
 |
Colin
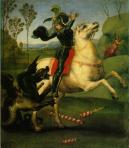
Location: Wellington
|
Posted: Tue Jan 09, 2007 9:09 am |
|
|
Either that or Nigel gets good with a smithy and hammers the lugs (and blade) from bar stock  |
|
|
 |
Angel
Site Admin
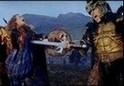
Location: Wellington
|
Posted: Tue Jan 09, 2007 9:12 am |
|
|
Always a valid option  _________________ Recognise anyone? Flame Warriors |
|
|
 |
Bogue
Sponsor
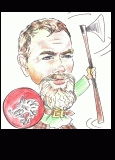
Location: Palmy
|
Posted: Tue Jan 09, 2007 8:13 pm |
|
|
One option for the manufacture and afixing of the lugs would be to get them welded professionally prior to getting the ht done.
If they are properly welded (Good penetration, right current range etc)
and then normalised it should be OK
(The component to be normalised is heated at temperatures around 40°C above the critical temperature for the particular metal alloy and soaked for several hours. Cooling in still air avoids large grain size occurring due to atomic diffusion. The resultant fine grain structure is stress free and the mechanical properties generally show a decrease in overall hardness, altered ductility and increased overall toughness, i.e. impact strength. http://hsc.csu.edu.au/engineering_studies/lifting/2521/Normalising.html )
If you get the blade hardened and then tempered once it has been normalised it should maintain its structural integrity.
Hey Colin can you give us some sort of idea as to what weight you should be looking at for a blade of this size.
I've done a couple of blades with 1200mm blades and the damn things came out to about 7lb (They did have 2mm edges because of their intended use thereby effecting the weight)
Cheers
Bogue |
|
|
 |
Colin
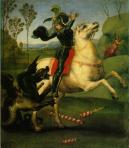
Location: Wellington
|
Posted: Wed Jan 10, 2007 6:41 am |
|
|
According to Wallace Collection Catalogues: European Arms and Armour, Vol. II the entire sword should weigh 4.5 pounds. I'm wondering if that's a misprint though.
According to http://www.thearma.org/essays/2HGS.html you're looking at 5 to 8 pounds for the entire sword.
What I've seen of European re-enactor's swords (from the continent, not UK), is they deeply hollow ground them. These ones have 2mm edges. |
|
|
 |
knight of magdalene
This account is inactive
|
Posted: Wed Jan 10, 2007 9:37 am |
|
|
A few points regarding sword construction. The deap grooves are called fullers, these are made in a variety of shapes from v's to u's and were about weight, not blood. Also remember that your trying to reproduce from a single spring bar something that was a little more complicated. Ie general (separate from damascus) sword construction ( in reality) consists of a minimum of two elements, the soft inner and the hard outer . One folded over the other. this enables the blade to be finer and as such lighter. Carbon is introduced during the making stage to only the outer layer. Using the spring steel is a cheap shortcut that works well for reenactment blade play but is not authentic and also has issues pertaining to brittleness should you harden the whole thing as per a real weapon. When hardening, let the colour come only to the part you want hardened (edge) other wise the hardening will run in to the distance. I prefer to temper the steel, and then cold harden the edges using a hammer and anvil on a cold morning tapping lightly hundreds of times on the cutting edge. It makes for a finer blade (when including the deap fuller with soft inner and hardened outer. It is a cheat and is not authentic insofar as it will be destroyed by an authentic blade yet will put nicks in the standard reenactment blade. |
|
|
 |
White Knight
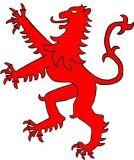
Location: Orcland
|
Posted: Fri Jan 12, 2007 12:44 am |
|
|
Boque what was meant by saying that to normalize the component the metal alloy was soaked for several hours and in the next sentence it talked about cooling in air? The two contradict. One would produce large grains and the other would produce fine grains.
Is there a stage betwen the soaking and cooling by air that is supposed to happen?
Can someone please help to clarify things?
Thanks. |
|
|
 |
Colin
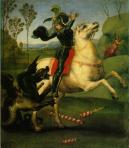
Location: Wellington
|
Posted: Sat Jan 13, 2007 3:24 pm |
|
|
If you do go the normalising route, get someone who knows what they're doing to do it. If should be safe enough for the lugs given that they're not high stress points on a blade.
The welding rods will need to be spring steel given that you're welding spring steel to spring steel, and presumably wanting to harden and temper afterwards.
You're biggest danger is that the welding process might crack the blade, and no amount of normalising will fix that. The cracks may or may not be visible to the naked eye. |
|
|
 |
Bogue
Sponsor
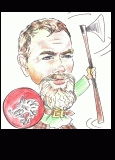
Location: Palmy
|
Posted: Sat Jan 13, 2007 5:23 pm welding spring steel |
|
|
As stated when I first mentioned normalising.
GET THE WELDS DONE PROFESSIONALLY. (I think the process you are after is called eutectic welding)
The expense of getting your welds x-rayed may make that part cost-prohibitive, but thats up to you.
As most of the shaping would quite probably be done after the fitting of the lugs and the grinding of the lug edges would be incorporated into the actual grind of the blade there shouldn't be too many problems with fractures apart from those inherent in the steel itself and there isn't a thing you can do about that.
A big thing to remember is make all internal corners rounded this will reduce the likelihood of fracture across those points.
hope that is of some help |
|
|
 |
Bogue
Sponsor
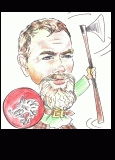
Location: Palmy
|
Posted: Sat Jan 13, 2007 5:35 pm |
|
|
White Knight wrote: | Boque what was meant by saying that to normalize the component the metal alloy was soaked for several hours and in the next sentence it talked about cooling in air? The two contradict. One would produce large grains and the other would produce fine grains.
Is there a stage betwen the soaking and cooling by air that is supposed to happen?
Can someone please help to clarify things?
Thanks. |
The link I posted explains the process.
But I shall post the information for simplicity sake.
From Aboutmetals.com
Normalising
Definition: A heat treatment process that has the object of relieving internal stresses, refining the grain size and improving the mechanical properties. The steel is heated to 800-900oC according to analysis, held at temperature to allow a full soak and cooled in still air.
My apologies for the length and images have been removed
from HSC online Charles Sturt University NSW
http://hsc.csu.edu.au/engineering_studies/lifting/2521/Normalising.html
Introduction
Lifting devices in their various forms are constructed from a range of materials that have specific properties for the function they will perform. The inherent structure that provides these necessary properties may not be capable of meeting a range of “working demands”. It is then necessary to enhance these properties by some means.
Alloying, cold working processes and heat treatment are ways of altering the structure of a material to improve its properties. These structure-altering procedures are often employed in combination to achieve the desired results.
For example, iron alloyed with carbon produces steel that is further enhanced with other metals such as molybdenum, chromium and vanadium.
The forging process will again change the properties, as will heat treatment.
Normalising
The heat treatment process of normalising is an excellent example of how the structure/property relationship is controlled to produce a component that functions with optimum reliability over a range of working-environment conditions.
The normalising process is a simple one that follows the basics of process annealing (used for stress-relieving of welded structures and large castings) but the cooling process occurs in still air rather than in the furnace.
The component to be normalised is heated at temperatures around 40°C above the critical temperature for the particular metal alloy and soaked for several hours. Cooling in still air avoids large grain size occurring due to atomic diffusion. The resultant fine grain structure is stress free and the mechanical properties generally show a decrease in overall hardness, altered ductility and increased overall toughness, i.e. impact strength.
Cold rolling and casting are forming processes that produce grain structures that may require normalising before the component is put into service.
Normalising at the correct temperature and for the right amount of time will modify these structures to produce a microstructure showing fine equiaxed grains as seen in Fig. 3
Normalising can soften, harden or stress relieve a material depending on its initial state and chemical composition. For example, a normalised 0.4%C steel will have a tensile strength of 580 MPa compared to an annealed steel of 510 MPa. Its ductility will be 27% compared to 30%, and its hardness will be 165 BHN compared to 145 BHN. That is, the normalised steel will be stronger, and harder, but slightly less ductile than the annealed steel. |
|
|
 |
Azash
Location: Kawerau
|
Posted: Fri Jun 01, 2007 9:54 pm A little clarification. |
|
|
In the hope that this is not too late..... I ahve not been following this site for way too long..... I am a engineering tutor and can assure you that :
1) Bogue the grain size is actually large when the item is normalised and when the item has been hardened and tempered the grain structure is small.... fine grains = hard metal
2) the soaking of the metal is to hold the metal heated at over the critical range for a period of time, professionally in a furnace this is done for around 2hours at 880 degrees C.
3) yes if the lugs were welded on then you need to normalise or anneal the whole of the blade, this will egualise the stresses in the metal caused by the welding processes...... by the way please done even dream of cooling the project at all or in any way after welding, that will harden it and possibly crack it. Then when the whole project is hardened and tempered it will all happen evenly. By the way.... annealing is cooling the project in the furnace (as slowly as possible, usualy turn the furnace off and come back in a week) were as normalising is cooling the project just in the open air, at its normal rate.
I do hope that this information is not too late for the project and if you want to talk to me further about this feel free to. I also do have access to the welders to be able to do this project and have recomendations for the correct welder as well..... but rest assured you will need to be sure that you use spring steel as the filler metal for the welds, so therefore it can not just be mig welded and low hydrogen rods do not contain the correct metal either. _________________ If at first you dont suceed then smack them again...... harder harder.... harder I say. |
|
|
 |
|