|
Author |
Message |
Boyd
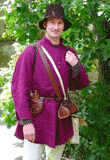
Location: London
|
Posted: Tue Sep 16, 2008 10:48 pm |
|
|
Thanks - lets hope I can pull it off
I think I need less than one medium sized cow horn.
I was able to get 6 panels out of 1 quarter of a horn.
I have decided to do 12 smaller panes rather than 8 larger panes on my lantern - it looks nicer!
_________________ Experience is not what happens to a man; it is what a man does with what happens to him.
Aldous Huxley in "Texts and Pretexts", 1932 |
|
|
 |
amuckart
Location: Wellington
|
Posted: Wed Sep 17, 2008 11:07 pm |
|
|
Nice work. I have a bag of horn in the garage and a bunch of brass sheet waiting to be turned into a lantern. One day, too much to do in the meantime and I've been totally unable to make anything for a couple of months now. Sucks.
Boyd wrote: | The conceptual plan for the lantern is attached. Planned to be Dia. 90mm and about 230mm high
|
That looks pretty good. From the extant ones I've seen with doors intact though the top of the door is flat and level with the bottom of the decorative arch bits rather than following the curves. There's a very nice example in The Medieval Household which I stronly recommend tracking down if you don't already have a copy.
_________________ Al Muckart. Shoe geek.
http://wherearetheelves.blogspot.com |
|
|
 |
Boyd
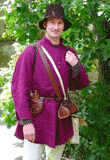
Location: London
|
|
|
 |
Oskar der Drachen

Location: Masterton
|
Posted: Sun Oct 05, 2008 8:51 pm |
|
|
Nice idea using the copper wire for the rivets. What was the source of this? I'm guessing solid core electrical supply with the coating stripped off?
You might try a rivet forge if you are going to do this in any great quantity.
Get two sections of square steel bar stock and clamp them together. Drill a hole the same diameter of the wire between the two halves. Each section of bar stock will have half the hole in it, the depth of the rivet length you want.
Cut a section of the copper wire slightly longer than the rivet you want, and insert it in the hole in the clamped forge, and peen the exposed end. Take the forge out of the vice, and you have a rivet.
I built one like this to make rivets for helmet making out of 5mm mild steel bar stock. I used to heavy sections of angle iron.
|
|
|
 |
Boyd
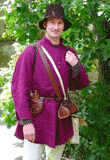
Location: London
|
Posted: Mon Oct 06, 2008 7:37 am |
|
|
Hiya
The copper was one of the many bits and pieces that I grab and have put away over the years! It was about dia. 3mm and maybe 1000mm long.
All I did for the rivets was heat the copper using an O/A welding torch. I held it up side down and it will burn green then spark and start to melt a bit when a nice little ball had formed I cooled it by quenching then cut it off the bar stock. It was easy and very quick. Plus the copper isn't overworked by the time I come to peen them over.
Regarding your rivet forge - when I have tried doing such with brass rivets I find they just expand into the hole and get stuck. and trying to push them out using the bar stock doesn't work. Admittedly was that only 2-3mm stock again.
_________________ Experience is not what happens to a man; it is what a man does with what happens to him.
Aldous Huxley in "Texts and Pretexts", 1932 |
|
|
 |
Oskar der Drachen

Location: Masterton
|
Posted: Mon Oct 06, 2008 5:28 pm |
|
|
Aha!
You have to make your forge in two pieces. These two sections are clamped in a vice, and the rivet formed. Then when you undo the vice the rivet falls out from between the two sections of the forge.
I'll have to take a couple fo pictures of the one I made. I went to the extra step of making a spring handle that was connected to both of the halves, and holds them slightly apart.
When you clamp the vice, the halves come together to make rivets, when you undo the vice, the forge opens under it's own spring-handle, drops the rivets out, and then the vice is closed agiain ready for more blanks.
|
|
|
 |
amuckart
Location: Wellington
|
Posted: Mon Oct 06, 2008 5:46 pm |
|
|
From what I've read of these in the context of making rivets for armouring it pays to put a shim between the two faces of the rivet vice before you drill the hole. It doesn't need to be thick 0.5mm or so, but that way it is guaranteed to grip the bar stock you feed it tight. The ones I've read about are drilled right through though so you can make rivets of any length, or mushroom over the end of a rod if you want etc.
_________________ Al Muckart. Shoe geek.
http://wherearetheelves.blogspot.com |
|
|
 |
Oskar der Drachen

Location: Masterton
|
Posted: Mon Oct 06, 2008 8:25 pm |
|
|
Very True! I read the same thing.
What I found though was that it was very difficult to get a straight, clean hole all the way through the facing blocks. It tended to drift off so that the hole wasn't cleanly through both faces. Even in a proper machine shop with a hefty drill press.
I also found that the one that I did get to go cleanly through, still did not grip the rod I was trying to put a head on, it kept getting driven through the hole. This might be an error of my technique, and I was trying to do it with 5mm steel bar instead of copper. I did not try heating the end of the rivet to be forged. I did not have the appropriate heat source.
What served my efforts best was a hole drilled to the depth I wanted my rivets to be as long as, and the same diameter as my rivet stock. With this configuration I was able to do all my work cold, and with consistent results.
The copper that seems to be used here is of such small diameter, I think a shim would give too much gap, and would result in a flange under the head of it as the metal was pressed into the gap.
|
|
|
 |
Boyd
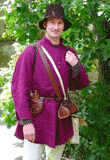
Location: London
|
|
|
 |
Bogue
Sponsor
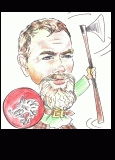
Location: Palmy
|
Posted: Sat Oct 18, 2008 8:30 pm Brass and horn Lanthorn |
|
|
Boyd:- That is just beautiful.
Awesome bit of work.
Bogue
|
|
|
 |
Boyd
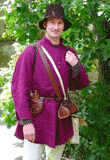
Location: London
|
Posted: Sun Oct 19, 2008 9:33 am |
|
|
Cheers!
_________________ Experience is not what happens to a man; it is what a man does with what happens to him.
Aldous Huxley in "Texts and Pretexts", 1932 |
|
|
 |
gt1cm2
Location: Wellington
|
Posted: Wed Jan 21, 2009 6:43 am |
|
|
Boyd, what is the cider vineger for? Is it a softening agent or to stop fungus buliding up in the water? I currently have some horn soaking but without the vinegar.
_________________ did they beat the drums slowly
did the play the fife lowly
did they sound the death march as they lowered you down
did the band play the last post and chorus
did the pipes play the flowers of the forest |
|
|
 |
Boyd
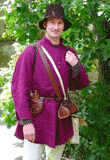
Location: London
|
Posted: Sun Jan 25, 2009 11:09 am |
|
|
Hiya Cindy - I am cut off from the internet at home and Our attempts to hook up to Xnet have been fruitless! It is like missing one of my senses! I have also replied by PM
I just like cider vinegar is all!
I think I initially used it as a gentle bleach and disinfectant. I did however boil those horns so it covered a little of the smell
I am trying to water soften by soaking the horn (nearly 3 months) in water that I have changed quite frequently as it gets a bit nasty but other than the bit near to where the horn meets the head there is no noticeable change in the rest of the horn.
What has happened is that where there are existing cracks or delamination in the horn these have split apart and can be pulled off by hand.
However it may require up to a year of soaking for it all to become soft or delaminate enough to do that by hand!
So I am getting ready to boil it! I just need to find a manky pot from the recycling centre!
I hope that this helps!
Cheers
Boyd
_________________ Experience is not what happens to a man; it is what a man does with what happens to him.
Aldous Huxley in "Texts and Pretexts", 1932 |
|
|
 |
|